Ensuring uninterrupted access is a key consideration when investing in IT services. However, achieving this level of performance in enterprise IT can be challenging. Businesses must define the service levels required to support seamless operations and minimize the impact of IT disruptions on business continuity.
Two metrics in this evaluation are reliability vs availability. While often confused, these metrics address different aspects of system performance. Availability refers to how frequently a system is operational and accessible, whereas reliability assesses how consistently it delivers its intended function over time.
This guide will explain the differences between availability vs reliability, highlight their significance for business operations, and demonstrate how they can shape a robust and effective IT strategy.
Related article: Why Choose Cloud-Based Asset?
What is reliability, and how do you measure reliability?
Reliability is measured by how well an ITSM system performs its required functions under specified conditions. The reliability of a system is usually expressed as a percentage or a fraction of uptime.
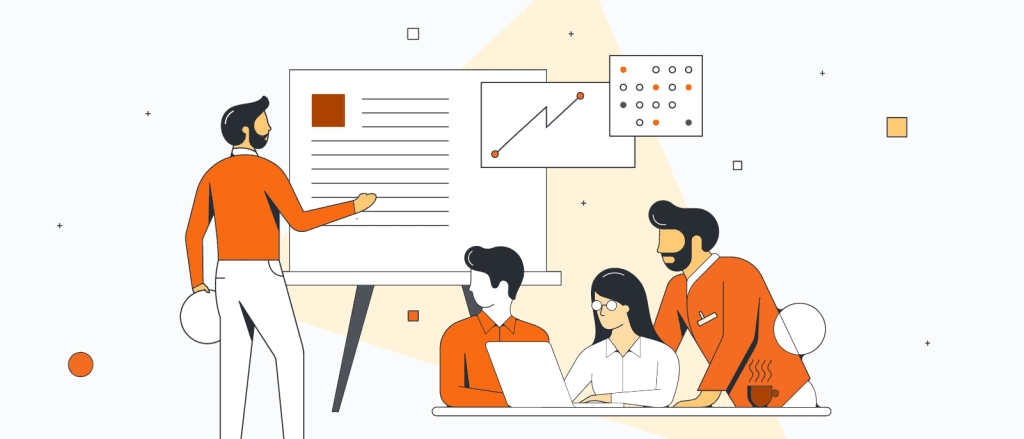
For example, if a system is operational 99% of the time, it is said to have a reliability of 0.99. Reliability is measured through several key ITSM metrics that help businesses assess the stability and dependability of their systems. Here are the most commonly used metrics to estimate system reliability
- Mean Time Between Failures (MTBF): This metric calculates the average time between system failures. A higher MTBF indicates better reliability, suggesting fewer system breakdowns over time.
- Failure Rate: This metric tracks how often failures occur within a specific time. Lower failure rates indicate better system reliability, meaning fewer user issues and smoother operations.
- Uptime Percentage: Uptime is when a system is operational and available. A 99.9% uptime ensures business continuity and indicates the system’s high reliability.
- Recovery Time (MTTR): Mean Time to Repair (MTTR) measures the average time it takes to restore a system after a failure. A shorter MTTR is a sign of a reliable system, as it can be quickly brought back online to minimize disruption.
- Error Rates: This metric tracks the number of errors or malfunctions in the system over a period. Lower error rates contribute to higher overall reliability, ensuring fewer performance issues.
What are the steps to improve Reliability?
You can improve the reliability of your systems with the following steps:
- Implement redundancy wherever possible. This means having multiple copies of critical data and components to make a backup available if one fails.
- Make sure all software and firmware are up to date. Outdated software can be a significant source of errors and instability.
- Perform regular maintenance on all hardware components. This includes cleaning dust out of fans and making sure all cables are firmly connected.
- Use high-quality components. Cheap components are more likely to fail than those built to last.
- Test your system regularly. It includes functional testing to ensure everything works and stress testing to see how your system behaves under extreme conditions.
What is availability, and what is the formula for finding availability?
Availability refers to the percentage of time a system, service, or component is operational and ready for use. It indicates a system’s reliability and performance over time, with higher availability showing minimal downtime and better overall service. High availability is crucial to ensure continuous operations and a smooth user experience. To calculate availability, you can use the following formula:
Availability = (Total operating time – Total downtime) / Total operating time |
This formula can calculate availability for any period, whether an hour, a day, or a week.
Suppose you calculate a website’s availability over a week. The website was operational that week for 168 hours (24 hours x 7 days). However, it experienced 2 hours of scheduled maintenance and 4 hours of unscheduled downtime, resulting in a total downtime of 6 hours.
Using the availability formula, the calculation would be:
Availability = (Total operating time – Total downtime) / Total operating time
Parameter | Value |
Total Operating Time | 168 hours (7 days × 24 hours) |
Total Downtime | 6 hours (2 hours scheduled maintenance + 4 hours unscheduled downtime) |
Uptime | 168−6=162168 – 6 = 162 hours |
Availability | 162168×100=97.6%\frac{162}{168} \times 100 = 97.6\% |
Result: The website’s availability for the week was 97.6%.
By calculating availability, organizations can gauge the effectiveness of their systems, ensure minimal disruptions, and maintain high levels of service.
Understand your current availability measurement. You can improve your availability once you know where you are and where you want to be.
● Set an achievable target. It’s necessary to decide on an attainable target. You should benchmark yourself against comparable offices in your industry. You can change your current plan requirements once you know how well others are doing in your industry.
● Ensure that systems are designed for availability. That involves incorporating features such as failover and redundancy into the system design.
● Monitor systems closely and identify potential problems before they cause downtime.
● Establish a good incident response plan to resolve issues quickly and efficiently.
Improving availability with better gear can be challenging as many factors, such as the current plan of your office framework, can take time to process purchase orders. Another factor is that most resistance to gear accessibility comes from operational procedures, not maintenance practices. Thus, you should be focused on ensuring any operating procedure doesn’t hinder your assets and performance.
Finally, you should increase availability through proactive maintenance. Proactive maintenance ensures that assets are dependable and available. Reactive maintenance is done when an asset has crashed, decreasing its availability. Implementing proactive maintenance practices is crucial to improving reliability. Whenever a breakdown occurs, it impacts availability as the asset cannot work on schedule. Additionally, downtime increases because of this broken state.
Reliability vs. Availability: Key Differences
- Definition:
Reliability refers to the ability of a system or component to perform its intended function over time without failure consistently. It measures how dependable the system is during operation.
Availability refers to the time a system is operational and accessible for use. It measures whether a system is up and running when needed.
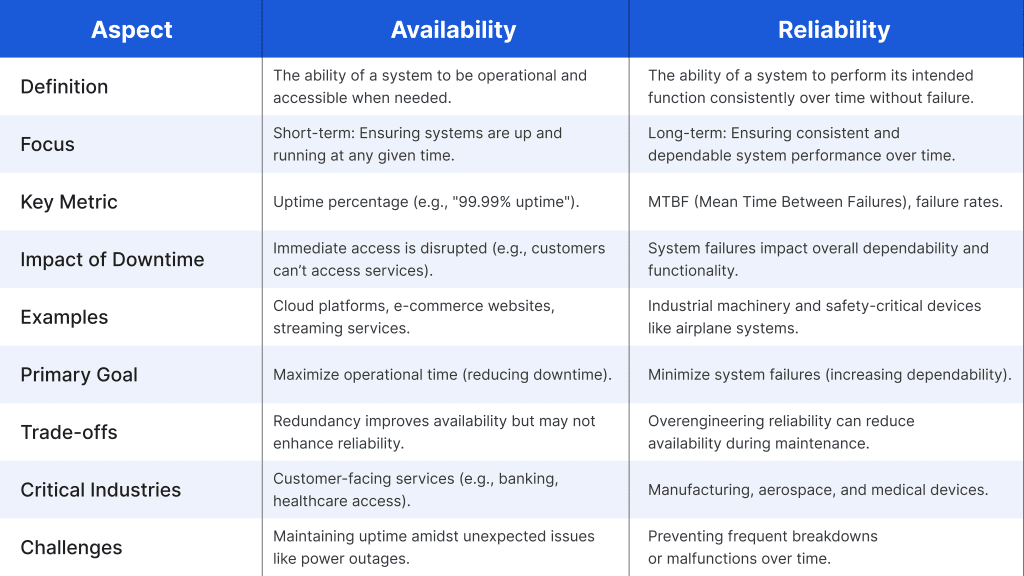
2. Focus:
Reliability focuses on the system’s long-term performance and consistency. It addresses how well the system performs its functions without breakdowns or failures.
Availability focuses on the system’s uptime and readiness for use. It assesses how often a system is operational and ready to perform its tasks.
3. Measurement Metrics:
Reliability is measured using metrics like Mean Time Between Failures (MTBF), failure, and error rates. A higher MTBF and lower failure rate indicate better reliability.
Availability is measured using uptime percentage and Mean Time To Repair (MTTR). A higher uptime percentage means greater availability.
4. Impact of Failures:
Reliability minimizes system failures over time, ensuring the system operates smoothly without unexpected breakdowns.
Availability deals with minimizing downtime and ensuring that the system remains accessible, even if parts of it fail. It’s about having the system up and running when needed, even if reliability is compromised.
5. Example:
Reliability Example: A server that consistently runs without crashing for extended periods is considered reliable.
Availability Example: A website accessible 24/7, even during server maintenance or temporary failures, is highly available.
Summary:
- Reliability is how well a system performs its intended function without failure over time, while availability is how often a system is ready and accessible. Both are critical for ensuring seamless operations, but they focus on different aspects of system performance.
Challenges in Managing Availability and Reliability
- Complex Infrastructure: Managing multiple systems, servers, and networks can make it challenging to maintain consistent performance. A failure in one component can trigger cascading issues affecting availability and reliability.
- Unforeseen Failures and Downtime: Unexpected hardware failures, software bugs, or external events like power outages can disrupt service availability and performance, making it difficult to predict and prevent downtime.
- Resource Constraints: Limited budgets, hardware, or personnel can force organizations to prioritize one aspect—availability or reliability—over the other, leading to potential trade-offs in system performance.
- Human Error: Mistakes in configuration, maintenance, or operations can introduce vulnerabilities or outages, affecting systems’ reliability and availability.
- External Dependencies: Relying on third-party services or vendors introduces risks. Downtime or performance issues from external providers can directly impact your system’s availability and reliability.
Conclusion:
Availability and reliability are essential factors to consider when determining the maintenance needs of a system or component. Availability measures how often a system or part can perform its required function. At the same time, reliability measures how frequently a system or component performs its required function correctly. Both measures are crucial when planning maintenance activities, as they can help to identify potential problem areas and determine the best course of action to take to prevent or mitigate problems.
FAQs
1) Why Are Availability and Reliability Important?
- Minimizing Downtime: Reduces disruptions to operations, preventing productivity losses and ensuring smooth business continuity.
- Enhancing Customer Satisfaction: Ensures services are consistently accessible, building trust and improving user experience.
- Protecting Brand Reputation: It avoids the negative impact of outages and showcases professionalism and reliability to customers and partners.
- Reducing Financial Losses: Prevents revenue loss, SLA penalties, and recovery costs associated with system failures.
- Supporting Critical Industries: It is essential for healthcare, finance, and manufacturing sectors, where interruptions can have severe consequences.
2) How does practical incident management impact the availability and reliability of a system?
- Rapid Issue Resolution: Downtime is minimized by quickly identifying and addressing incidents and improving system availability. Faster resolution times also mean the system can return to its normal operational state more quickly, enhancing reliability.
- Proactive Monitoring: Incident management often involves continuously monitoring systems to detect potential issues before they escalate into major problems. This proactive approach helps maintain high availability and reliability by preventing unexpected failures.
- Root Cause Analysis: Effective incident management includes thorough root cause analysis to understand why an incident occurred. By addressing the root causes in the future, organizations can prevent similar incidents, improving the system’s overall reliability.
- Documentation and Learning: Incident management processes typically involve detailed documentation of incidents and the steps to resolve them. This documentation is a valuable resource for learning and improving future responses, which can enhance both availability and reliability.
- Communication and Coordination: Efficient incident management ensures clear communication and coordination among team members, which helps resolve issues faster. This coordinated effort contributes to maintaining high availability and reliability.
By implementing robust incident management practices, organizations can ensure that their systems remain operational and perform reliably, even in unexpected issues.