Inventory management is one of the most important aspects of any business, and spare parts inventory management is no different. Spare parts management is the process of organizing, storing, and controlling spare parts and components inventory to ensure that they are available when needed and to avoid obsolescence. There are many factors to consider when managing spare parts inventory, such as lead time, minimum order quantity, storage space, and shelf life. Proper spare parts inventory management can help reduce downtime, improve customer satisfaction, and increase profitability. We will discuss spare parts management in detail in this article.
Spare parts inventory is a collection of parts and components that are used to repair or replace damaged equipment. This inventory is usually kept in a separate area from the main inventory and may be organized differently. So, how do we manage the spare parts inventory?
Related Articles: Inventory Management vs. Asset Management: Are they any different from each other?
What is Spare Parts Management?
Spare parts management is the process of anticipating the need for replacement parts and stocking them in a convenient location. It ensures that production can continue in the event of a failure and minimizes downtime.
Spare Parts Management is to provide the right parts, with the expected level of quality, in the correct quantity, to the right location, at the right time, and at the least total cost to the company”. Effective management of maintenance spare parts is vital to equipment operating performance and to justify the investment in maintenance. The scope of this service includes all functions from the supplier through to the point of use, i.e., identifying, classifying, procuring, stocking, supplying, maintenance, etc.
To be proficient at managing your spare parts inventory, you would need to understand how the stock of spare parts ties in with reliable operations. To ensure optimum efficiency, you must also adopt a practical and structured management process.
We will explore the various factors that increase efficiency in spare parts management.
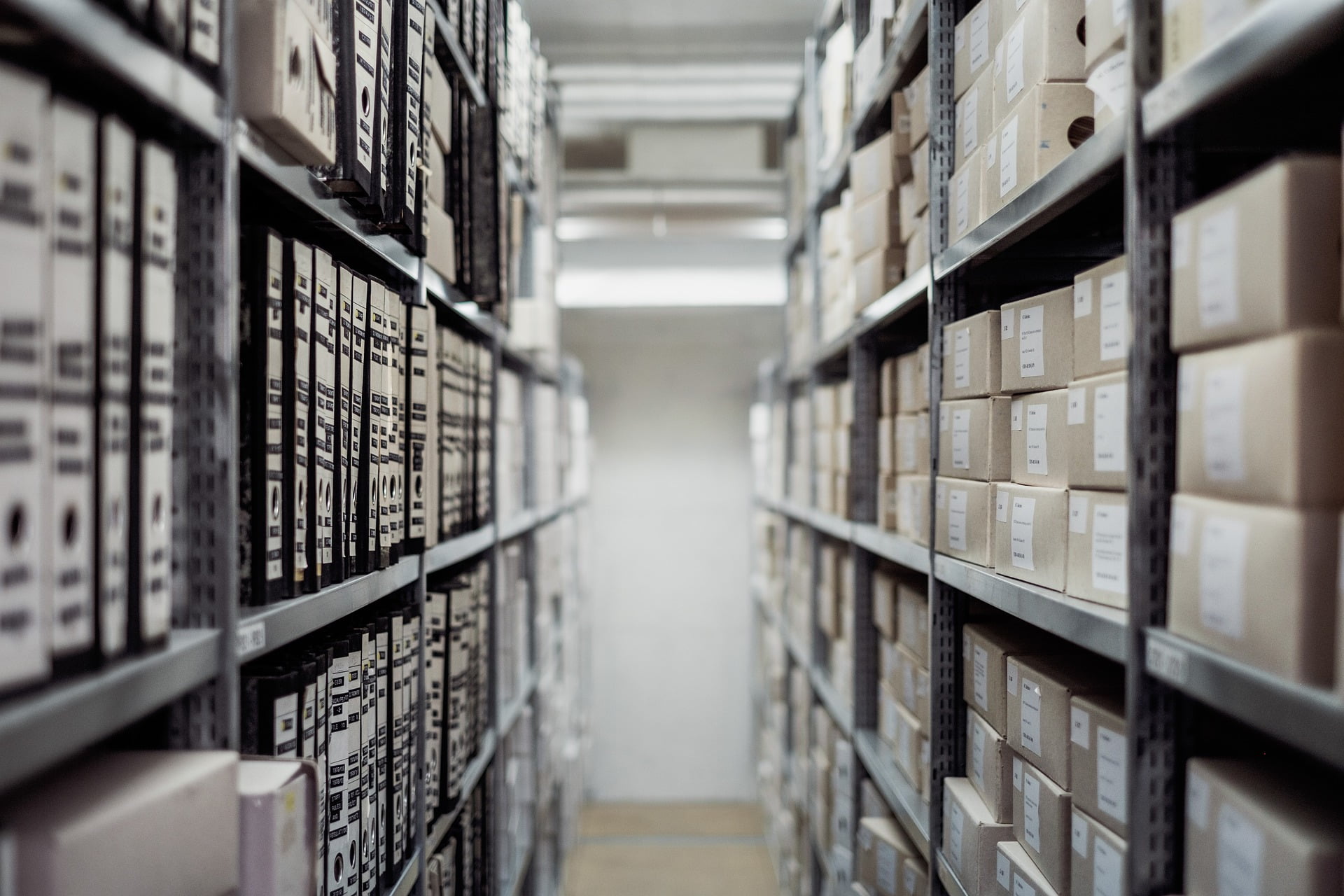
How to become efficient at spare parts management?
Here’s a list of areas to focus on to ensure efficient spare parts management and to have control over the stock. It is vital to categorize and define the spare parts in order of importance to prioritize the usage. Scheduled reviews of all spare parts based on replacements and frequency of change would be a good start. It will help you see if you have any excess stock of certain parts and less of another.
Inventory levels
Keep track of what you have in stock, as well as where those items are located. Have a good understanding of the types of spare parts that are required for your operation and how many of each type you will need, i.e., having the right amount of spare parts, not too few or too many.
Reorder points
Reorder points are the inventory level at which a company reorders more stock. Managing to reorder points efficiently can help ensure that a company has the spare parts it needs on hand while avoiding excess inventory and associated costs. An efficient spare parts management system will take into account lead times, demand variability, and other factors to determine the optimal reorder point for each spare part.
Lead times
Lead time is the amount of time it takes to receive a product from the time an order is placed. Managing lead times is essential as it can help ensure that spare parts are available when needed and that inventory levels are kept low. Lead time management can involve techniques such as order staging, just-in-time delivery, and lot sizing.
Safety stock
Safety stock is a way to maintain a buffer inventory to ensure that you don’t run out of stock when needed. The inventory is maintained to hedge against the uncertainty of demand and supply.
Security measures
Efficient spare parts management includes security measures with limited and authorized access to parts, physically securing the stock to prevent loss or theft of spare parts and to minimize the risk of damage.
Economic order quantity
The economic order quantity (EOQ) is the quantity of inventory a company should order to minimize the cost of the merchandise. The EOQ is the point where the company’s inventory costs are minimized. The company can either order too much inventory and incur storage costs or order too little inventory and incur opportunity costs. The goal of the EOQ is to find the point where these two costs are minimized.
Operating strategy with data analytics
To perform spare parts management successfully, you must adopt a predictive strategy. Successful maintenance management’s core lies in the ability to avert future problems. This scope includes locating and solving significant problems that may arise and using predictive management to optimize usage of resources, lessen cost, and reduce the time that is taken to resolve issues.
While companies may be aware of the need for efficiency in managing their spare parts inventory, they don’t always prioritize it in their daily operations. Failing to organize their inventory and following best practices can be more of a problem than they realize. Fortunately, you can leverage the software and tools available to be proactive in your spare parts management.
Related Articles: Benefits of Equipment Inventory Management Systems
Spare parts inventory management best practices
Spare Parts Inventory management is one of the most important aspects of running a successful business. Too much inventory can tie up your resources, while too little can lead to lost sales and unhappy customers. It would be best if you keep the following key factors in mind when managing your inventory:
Know what you have in stock.
This statement seems obvious, but it’s essential to have a system in place to track your inventory. You can use an Excel spreadsheet or an online database. You can also use a comprehensive solution to track, monitor, and manage your stock. It must include the following points:
- Keep an updated inventory of all spare parts.
- Cross-reference spare parts with equipment manuals.
- Label all spare parts clearly and consistently.
- Store spare parts in a clean and organized manner.
- Inspect all spare parts regularly for defects.
- Quarantine any defective spare parts.
Know what you need and when to procure
This ties in with the first point. You need to know what inventory you have on hand in order to know what you need to reorder. Reordering in a timely manner will mitigate the risk of losing sales. Waiting for an item to go out of stock cannot be an option. Conversely, if you have a stock surplus, you risk your inventory becoming obsolete.
Store your inventory properly
It includes both physical storage (e.g., shelves, bins, etc.) and digital storage (e.g., barcodes, QR codes, tracking numbers, etc.). It is crucial to make sure that it is well-organized and easily accessible. A digital inventory system can help you keep track of where each part is located, how many you have in stock, and when you need to order more. This can save you a lot of time and money in the long run.
Manage your inventory regularly
Review your inventory levels on a regular basis and adjust your ordering accordingly. You can avoid the cost of storing unnecessary parts. You can do this using a spare parts inventory system, preferably in the cloud, so that you can access it from anywhere on any device.
Following these best practices ensures that your spare parts inventory is managed effectively and efficiently.
Common questions on Spare Parts Management
When you decide to implement a Spare Parts Management solution, a few common questions will come up. The answers will help clarify the need for effective management, reduce operational costs, save time and resources, and justify the investment in deploying the right solution in your company.
Why are spare parts important?
Spare parts are essential because they provide a way to replace broken or missing parts on equipment. This can help keep the equipment running properly and avoid costly repairs or replacements.
Why is spare management important?
Spare parts management is vital because it ensures that the correct spare parts are available when needed and that those spare parts are in good condition. It can help to avoid disruptions in production and can improve the overall efficiency of the manufacturing process.
How do you manage your spare parts?
There are many ways to manage spare parts. The most common way is to use a spare parts inventory system. This system can be as simple as a spreadsheet or as complex as a computerized system. A comprehensive Spare Parts Management solution with automation and AI is the best choice for efficiently managing your spare parts inventory. The centralized system can help identify, locate, and manage your inventory, streamline your work processes, offer secure access to authorized users, and help you keep control of your spare parts inventory.
To conclude
Any business that depends on machinery or equipment to conduct its work must manage its spare parts inventory effectively. You can ensure that your spare parts inventory is properly handled and structured by adhering to the best practices described in this article, which will make it simpler to locate the spare parts you need when you need them.
The most crucial thing is for a business to invest in software asset management tools or automated inventory solutions. It can offer a company several benefits.