Introduction: The Importance of Inventory Audits
IT Inventory Audits are critical in ensuring that businesses maintain accurate records of their assets, reducing financial risks and operational inefficiencies. These audits help companies verify stock levels, prevent losses, and optimize resource allocation. Proper inventory management, supported by regular stock audits, contributes directly to profitability by reducing waste, preventing theft, and improving workflow efficiency.
Related blog: The Ultimate Guide to IT Asset Management: A Step-by-Step Checklist
What Is an Inventory Audit?
An inventory audit systematically verifies a company’s inventory levels, ensuring accuracy between recorded data and actual stock. It helps businesses identify discrepancies, improve stock control, and maintain compliance with financial reporting standards. Related terms like stock audit refer mainly to verifying physical inventory, which is crucial in industries dealing with tangible goods.
Types of Inventory Audits
Explain various audit types:
- Physical inventory audits: Counting items manually
A physical inventory audit involves manually counting all the inventory items to verify the stock levels. While being accurate, it’s time-consuming and disruptive to operations.
- Cycle counting: Regular checks on a portion of the inventory
Instead of counting the entire inventory at once, cycle counting involves regularly auditing a small subset of stocks. This approach reduces operational disruptions and allows continuous monitoring of the stock levels.
- System-based audits: Using an inventory system for tracking and cross-referencing
System-based audits leverage inventory management software to track stock movement and cross-reference system records with an actual inventory. This method increases efficiency but requires an updated and well-integrated digital system.
Benefits and limitations of each type
- Physical Audits: Highly accurate but time-consuming.
- Cycle Counting: Less disruptive but may miss errors in infrequent areas.
- System-Based Audits: Efficient but depend on technology accuracy.
The Inventory Audit Process: A Step-by-Step Guide
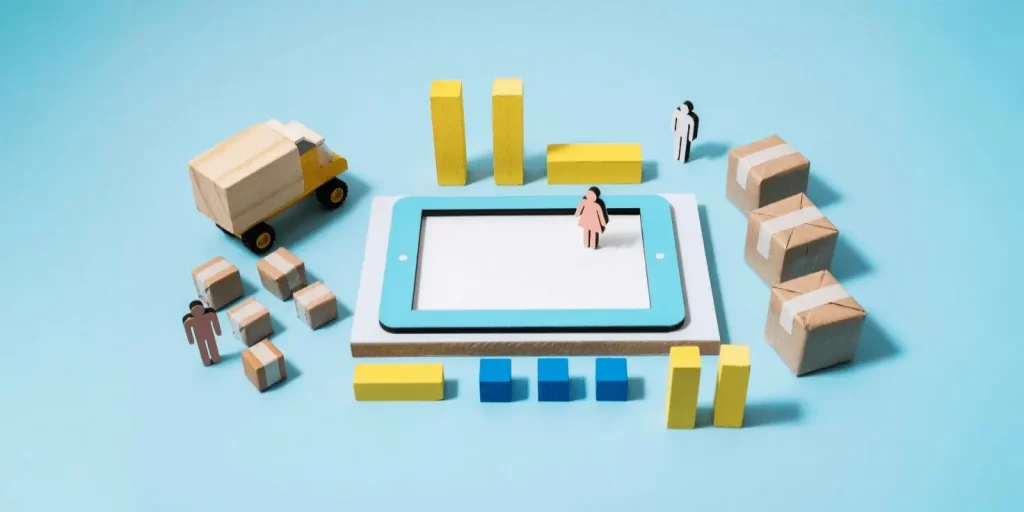
Key steps in conducting an inventory audit process:
- Planning and preparation
Before conducting an inventory audit, businesses should define the scope, assign responsibilities, and gather all the necessary tools like barcode scanners and tracking software.
- Establishing counting methods (manual vs automated)
Companies must decide between manual counting, automated tracking, or a hybrid approach to ensure efficiency and accuracy.
- Using technology like barcode scanners or inventory systems for efficiency
Utilizing inventory management systems with real-time tracking, barcoding, and automated reconciliations minimizes errors and speeds up the process.
- Analyzing results and resolving discrepancies
After data collection, auditors must compare recorded stock levels with actual counts, investigating discrepancies caused by theft, damage, or system errors.
- Reporting and documentation
A detailed report should summarize findings, highlight inconsistencies, and recommend corrective actions to improve inventory management strategies.
Tips to streamline the process and improve inventory accuracy
- Regular cycle counts should be conducted to identify issues early.
- Leverage automated inventory tools to minimize human errors.
- Train staff on best auditing practices for consistency.
Why Is Inventory Auditing Essential for Business?
Regular inventory audits improve stock control, reducing the risk of overstocking, understocking, and financial misstatements. They also help:
- Detect and prevent fraud or theft.
- Optimize supply chain management by identifying slow-moving inventory.
- Ensure compliance with financial and regulatory requirements.
Tools and Techniques for Effective Inventory Audits
The right inventory management tools enhance the inventory audit process by providing real-time tracking and reducing manual errors. Key technologies include:
- Barcode and RFID Scanning: Automates data collection for accuracy.
- Cloud-Based Inventory Software: Provides real-time stock updates and data synchronization.
- AI-Driven Analytics: Predicts inventory trends and prevents stock shortages.
Common Challenges in Inventory Audits and How to Overcome Them
Following are some of the common challenges in inventory audits and their solutions.
- Human Errors
Manual data entry and counting mistakes lead to inaccuracies.
Solution: Implement barcode scanners and automated systems to reduce reliance on manual input.
- Time Constraints
Full-scale audits can disrupt operations.
Solution: Adopt cycle counting to maintain accuracy without operational downtime.
- Outdated Systems
Old inventory tracking methods may lead to discrepancies.
Solution: Upgrade to modern inventory management platforms for real-time monitoring.
Related blogs: Leveraging IT Asset Insights for Smoother Banking Operations
Conclusion: The Value of Inventory Audits for Business Success
Incorporating regular inventory audits is essential for maintaining operational efficiency and financial accuracy. To streamline and enhance this process, leveraging advanced tools like Infraon’s asset management solutions can be highly beneficial. Infraon offers a comprehensive suite to optimize asset control and improve service efficiency. Our platform provides real-time tracking of IT assets, automated inventory discovery, and centralized dashboards for better visibility. By integrating Infraon’s solutions into your inventory audit process, businesses can achieve greater accuracy, reduce manual efforts, and ensure compliance with industry standards.