Introduction
Effective inventory management is vital for businesses to maintain smooth operations, control costs, and meet customer demands on time. Without proper tracking, companies risk stock shortages, excess inventory, poor inventory management or mismanagement, which can lead to financial losses.
Many companies with inventory face challenges like inaccurate demand forecasting, supply chain disruptions, and storage inefficiencies. These issues can slow down operations and affect profitability. By understanding these challenges and implementing smart solutions, businesses can optimize stock levels, improve efficiency, and enhance customer satisfaction. Exploring inventory management examples can help companies develop strategies to streamline their inventory processes and stay competitive in the market.
Related Blog: A Complete Guide to IT asset Inventory
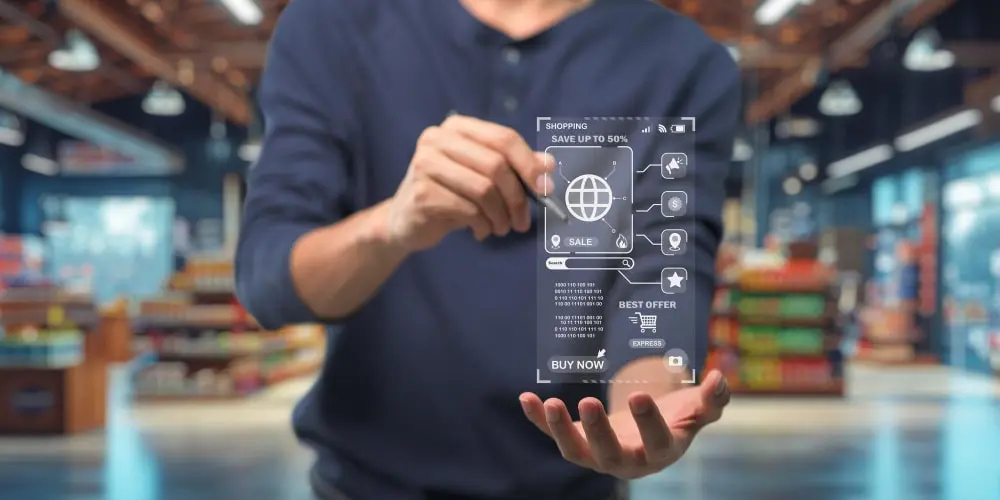
What is Inventory Management?
Inventory management is the process of tracking, storing, and managing a company’s stock to ensure the right products are available at the right time. It plays an essential role in business operations, helping companies maintain a balance between supply and demand while minimizing costs and waste.
Key Components of Inventory Management
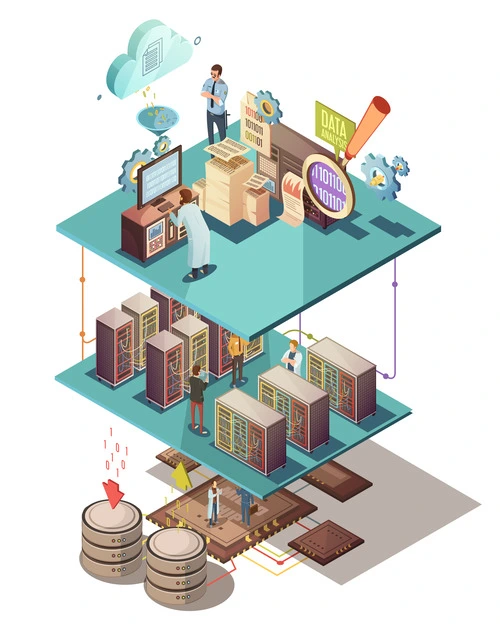
- Stock Control – Managing inventory levels to avoid overstocking or running out of essential products. Proper stock control ensures businesses can meet customer demand without unnecessary storage costs.
- Demand Forecasting – Predicting customer demand using past sales data, market trends, and seasonal changes. Companies with inventory rely on accurate forecasting to optimize purchases and prevent losses due to unsold stock.
- Supply Chain Coordination – Ensuring smooth communication between suppliers, manufacturers, and warehouses. A well-managed supply chain prevents delays and ensures timely restocking, keeping operations efficient.
Impact of Poor Inventory Management
When inventory is mismanaged, businesses face serious challenges. Overstocking ties up capital and increases storage costs, while understocking leads to missed sales and unhappy customers. These inventory management challenges can hurt revenue, lower customer satisfaction, and reduce overall efficiency.
By learning from inventory management examples and using smart strategies, businesses can streamline operations, reduce waste, and improve profitability. Strong inventory management is the backbone of a successful supply chain. It ensures smooth business operations and customer satisfaction.
Common Inventory Management Challenges Faced by Companies
Managing inventory efficiently is crucial for businesses to stay profitable and meet customer demands. However, many companies with inventory face difficulties in managing the different aspects. These inventory management challenges can lead to financial losses, wasted resources, and dissatisfied customers. Below are some common challenges businesses encounter.
1. Overstocking
Holding excess stock ties up capital and increases storage costs. Products may become outdated, expire, or lose value over time, leading to unnecessary losses. Effective stock control helps prevent over-purchasing and minimizes waste.
2. Stockouts
Running out of essential products can result in lost sales and unhappy customers. Customers may turn to competitors if businesses cannot fulfil orders on time. Proper demand forecasting and real-time inventory tracking can help prevent stock shortages.
3. Poor Forecasting
Inaccurate predictions of customer demand lead to overstocking or stockouts. Businesses need data-driven forecasting methods to balance supply and demand effectively. Looking at inventory examples from successful companies can help refine forecasting techniques.
4. Inefficient Warehouse Management
Disorganized storage and poor warehouse operations slow down order fulfilment. If employees struggle to locate products quickly, shipping delays occur, affecting customer satisfaction. Proper warehouse layout, automation, and real-time tracking can enhance efficiency.
5. Lack of Automation
Relying on manual stock tracking increases human errors, leading to inaccurate inventory records. Businesses should invest in inventory management software to streamline tracking, reduce errors, and improve operational efficiency.
By addressing these inventory management challenges, businesses can improve efficiency, cut costs, and enhance customer service. Smart inventory strategies ensure companies stay competitive and meet market demands effectively.
Poor Inventory Management Examples from Huge Brands
Inventory mismanagement can happen to even the biggest companies, leading to huge financial losses and operational failures. Whether it’s overstocking, stockouts, or supply chain disruptions, these mistakes highlight why businesses must invest in proper planning and execution. Here are some real inventory examples of famous brands that suffered due to inventory management problems.
- Nike’s $100 Million Inventory Forecasting Failure
Nike trusted an automated demand forecasting system to predict product demand, but it backfired. The system overestimated demand for some products while underestimating others. This mistake cost Nike $100 million in excess stock and shortages.
Lesson: Even the most advanced technology needs constant monitoring and proper management to avoid poor inventory management issues.
- Walmart’s Stockout Crisis (2013-2014)
Walmart decided to cut back on staff to save costs, but this led to major stock replenishment issues. Empty shelves meant lost sales and disappointed customers. Lesson: Reducing operational costs is important, but it should never come at the expense of inventory control.
- Target Canada’s Inventory Disaster (2013-2015)
Target’s expansion into Canada was a disaster because of poor supply chain planning. Warehouses were either overflowing with excess stock or missing essential products that customers needed. As a result, Target shut down its Canadian operations within two years, losing $2 billion.
Lesson: Before expanding, businesses must study inventory examples of successful retailers and ensure supply chains are well-structured.
- KFC’s UK Chicken Shortage (2018)
KFC switched suppliers to cut costs, but the new logistics partner failed to deliver chicken to stores on time. This forced over 900 UK stores to shut down temporarily due to stockouts. Lesson: Companies with inventory must ensure supplier reliability before making big changes.
- Boeing’s 737 MAX Production Halt (2019-2020)
Boeing underestimated supply chain delays for key aircraft parts, which led to a production halt for months. The company lost billions in revenue.
Lesson: Businesses should anticipate inventory management problems and have contingency plans to prevent disruptions.
These cases prove that even industry leaders can suffer from poor inventory management. By learning from their mistakes, businesses can avoid similar costly failures.
How Companies Can Avoid Poor Inventory Management
- Use Demand Forecasting for Accuracy: Predicting demand is crucial to avoid overstocking or stockouts. Studying past inventory management examples and using data-driven forecasting helps businesses plan better and maintain optimal inventory levels.
- Implement Warehouse Automation: Manual tracking increases the risk of errors. Automating warehouse operations with barcode scanners and real-time tracking software ensures better stock management and minimizes human mistakes.
- Maintain Safety Stock: Unexpected demand spikes or supply chain disruptions can lead to shortages. Keeping a small buffer stock ensures businesses can meet customer needs without delays.
- Choose Reliable Suppliers: A company’s inventory is only as good as its supply chain. Partnering with trusted suppliers with a proven record helps maintain consistent stock levels and prevents disruptions.
- Regular Inventory Audits: Frequent stock checks help identify discrepancies and prevent losses due to miscounts, theft, or system errors. Regular audits ensure inventory records match actual stock levels.
By following these strategies, companies with inventory can avoid costly mistakes and ensure smooth, efficient operations.
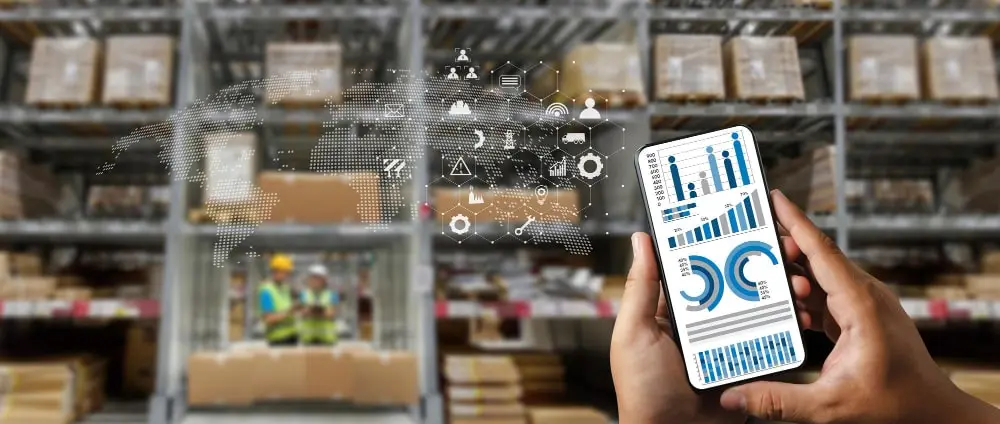
Conclusion
Even the biggest brands have faced costly failures due to inventory management challenges. From Nike’s forecasting failure to Walmart’s stockout crisis, these inventory management examples show how poor planning, supplier issues, and inefficient tracking can disrupt operations, lead to huge financial losses, and damage customer trust.
To avoid these inventory management challenges, businesses must adopt smart strategies to maintain the right balance of stock and ensure smooth operations.
The key takeaway? Companies with inventory must prioritize smart inventory practices, use reliable forecasting methods, and ensure supply chain efficiency. Learning from past mistakes helps businesses prevent similar failures and stay competitive.
This is where Infraon comes in. As a trusted name in inventory management, Infraon offers advanced solutions that help businesses maintain accurate stock levels, optimize supply chains, and prevent costly disruptions. Its efficient tracking, real-time insights, and automation ensure that inventory runs smoothly without errors or wastage.